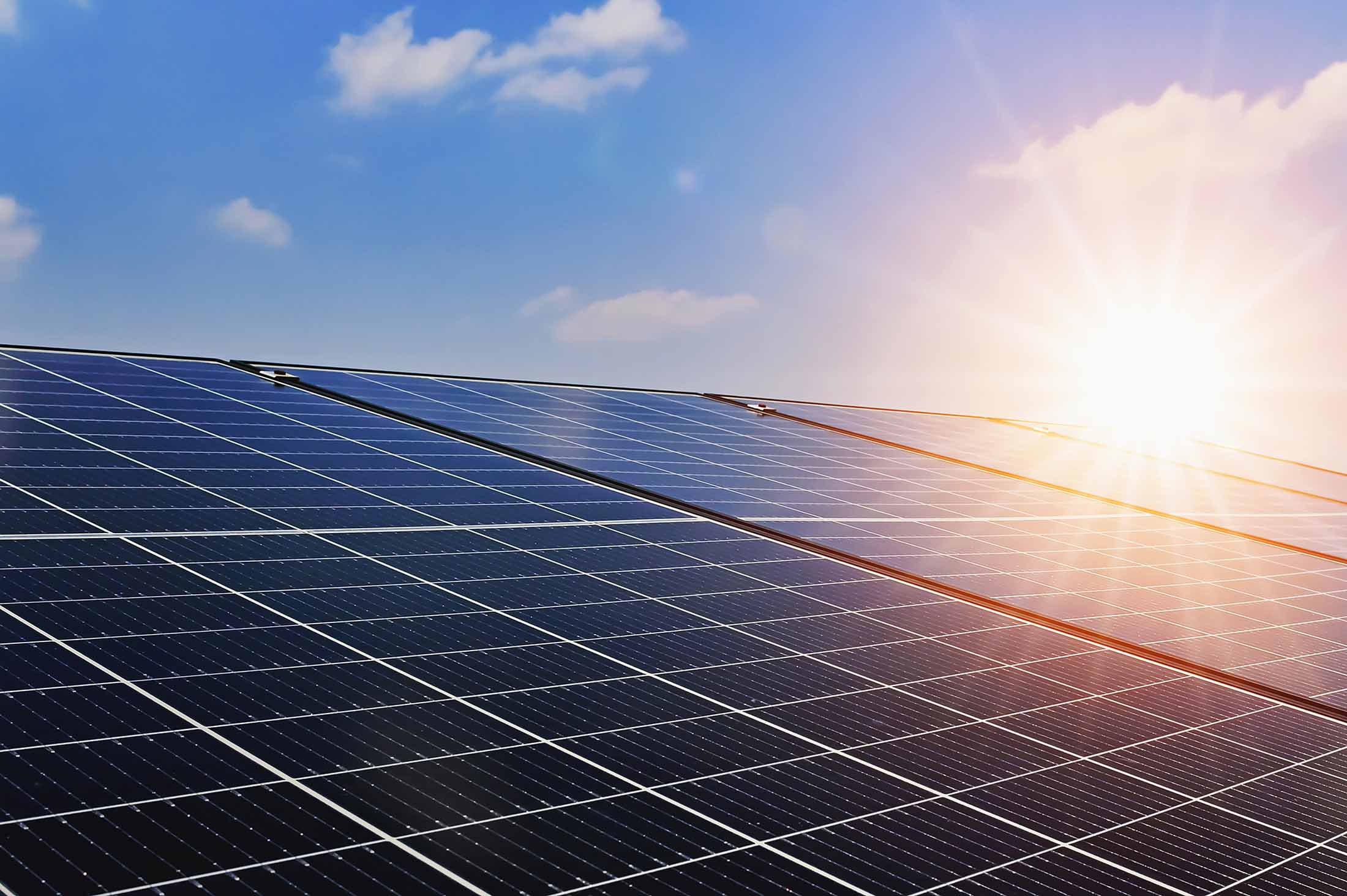
UNSW researchers find critical failures in latest solar panel technology
PV module failures caused by poor materials could jeopardise the government's Solar Sunshot program without a better testing hub.
The federal government’s $1 billion Solar Sunshot program could be undermined from the very beginning if it doesn’t include a crucial piece of infrastructure: materials testing.
This is the message coming from a team of researchers at the University of New South Wales (UNSW), who are finding critical failures in the latest solar panel technology caused by suppliers’ different recipes for the base materials.
UNSW professor Bram Hoex sees this as an opportunity, as he investigates whether his lab at the School of Photovoltaic & Renewable Energy (SPREE) – which already does specialist, small scale testing for solar panels – could become the national testing hub for the new industry.
He says major solar panel manufacturers in China already have their own quality assurance labs to certify materials suppliers, but it would be far too expensive for smaller manufacturers in a future Australian industry to do the same.
“If we centralised that and made sure there is a place in Australia where we have this supply chain checking, available to all Australian companies, that would be ideal,” he told RenewEconomy.
“Unfortunately, the more efficient your solar panels become, the relative impact of problems becomes larger as you approach the fundamental limits of materials, as we are with silicon.
“The supply chain is the main risk. If your supplier changes a little bit in manufacturing you would potentially not know and it would not require recertification, but that could actually introduce these failure modes.”
The SPREE researchers’ latest paper has found that material supplied by one manufacturer to a solar panel maker is causing power losses of up to 65 per cent in the latest solar panel technology – TOPCon (Tunnel Oxide Passivated Contact) — which is expected to be the dominant product in global markets from this year onwards.
A maximum of 20 per cent performance loss over a panel’s lifetime is generally seen to be the ideal.
Hoex is looking at how much investment would be needed to expand the current testing facilities, but says tools alone would cost in the realm of $200,000 to $300,000.
More ways to fail
Hoex’s team has been investigating the problems with TOPCon and HJT (HeteroJunction Technology), both of which have overtaken PERC (Passivated Emitter and Rear Contact) solar cells, for some time. Their research last year shows that both of the new high-tech panels are introducing new and as-yet not well understood ways to fail during manufacturing.
TOPCon panels are more complex than PERC as they have more layers and use more complicated technology. They also use a type of silicon that is harder to work with and require semiconductor-level clean rooms to manufacture.
The latest research focusing on TOPCon panels shows that changing suppliers for the same materials can radically alter how fast a panel deteriorates.
The latest paper is based on testing for an undisclosed panel manufacturer, which wanted to assess materials from different suppliers.
“We identified that in the POEs (polyolefin elastomers), which are typically seen as very robust encapsulants, some of the additives react so strongly with humidity and soldering flux they undergo a reaction. The failures we see are consistent with corrosion,” says Hoex.
“That results in resistance increases. If panels become so resistant [such as two examples that reached 65 per cent power loss], they can’t extract energy from the solar cell.”
Highly strung solar panels don’t like hidden chemicals
The experiment, at the international standard of 85°C and 85 per cent relative humidity, tested three PERC panels, one with an ethylene vinyl acetate (EVA) backsheet and two with POE backsheets made with materials from different suppliers.
Backsheets are used to seal and encapsulate the sensitive solar cells in a solar panel. They’re lighter than glass which means panels that use these are more useful, such as for rooftop solar.
Testing of the TOPCon panels added an extra backsheet supplier into the mix and two different options for POE.
The results were stark: changing suppliers for the less sophisticated – and less sensitive – PERC panels mean a drop in power of 1-2 per cent after 1000 hours of testing.
Changing suppliers for the more efficient, highly strung TOPCon panels created massive discrepancies, with the best panel only degrading by 4 per cent after 1000 hours, while the worst was basically non-functional at 65 per cent.
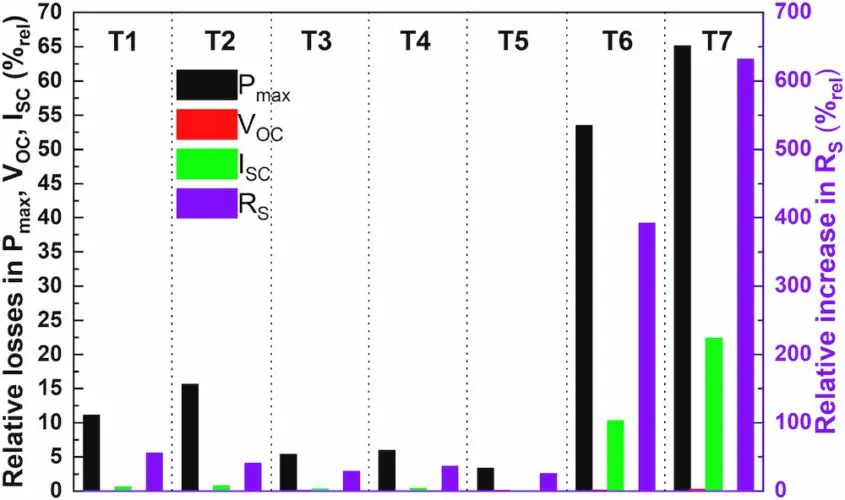
The failures happened in three areas: at a localised point, at connection points for ribbon wires and busbars, and for a whole module – which is what happened to the two worst performing panels.
The UNSW researchers think the first type of failure might be due to an electrochemical reaction between moisture, cell metallization, and contaminants likely present on the cells before encapsulation.
The second was probably from a reaction between moisture, ribbon wires, cell metallization, and soldering flux, which caused metal corrosion.
The last failure was likely a combination of these, plus a reaction with other, as yet unknown additives in the POE.
The next step for the research is to figure out what those extra additives in each POE backsheet were that are causing the problems.
“These findings underscore the critical issue associated with certain types of POE encapsulations and suggest that greater attention and detailed study should be exercised before selecting the type of encapsulation for TOPCon cells,” the paper says.