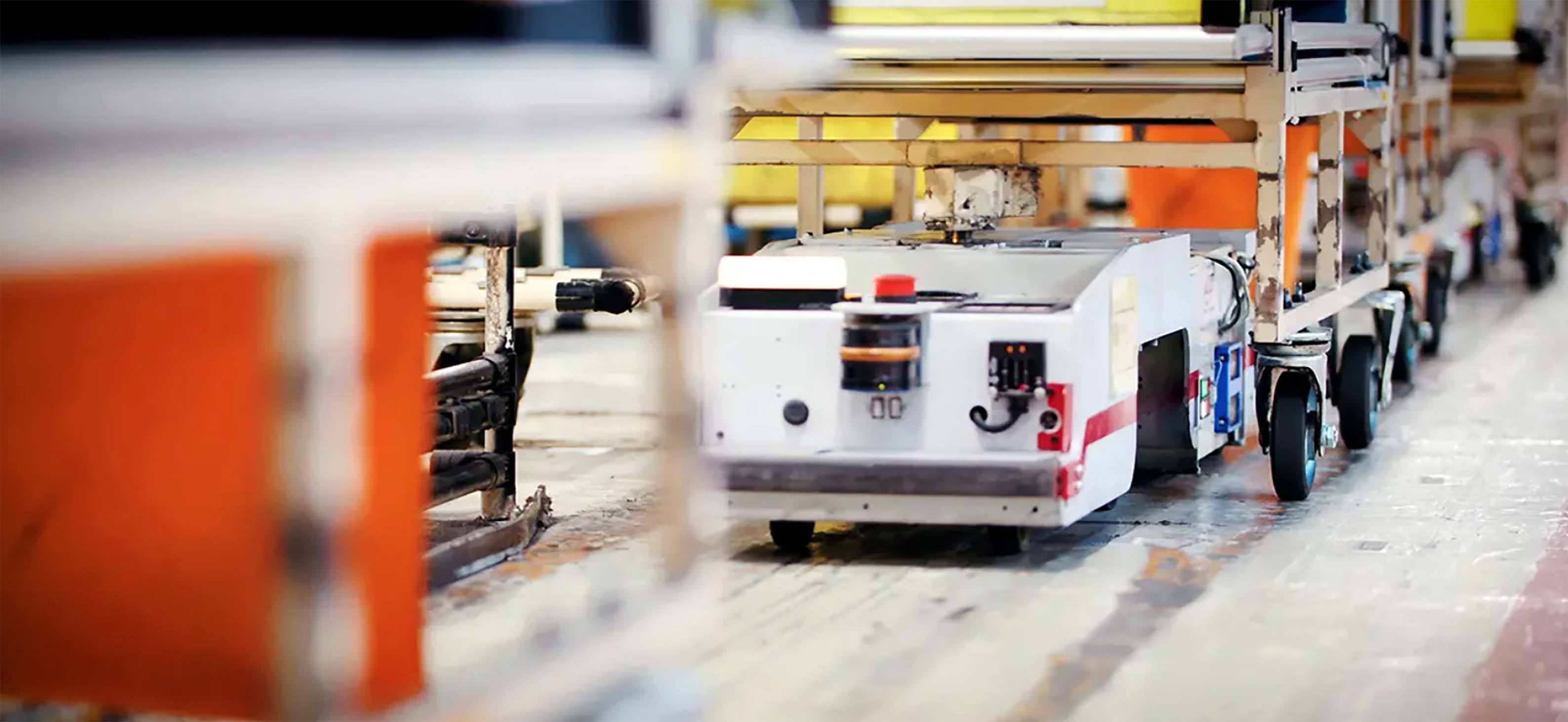
How the US EV battery recycling industry is gearing up
Battery recycling will be critical for the environment, human health and EV supply chains as tens of millions of batteries reach the end of their lives.
The US Inflation Reduction Act, now past its first anniversary, gives consumers and automakers in the United States a strong incentive to buy or sell a new electric vehicle (EV): a federal tax credit of up to $7,500.
But for vehicles to qualify for the full clean vehicle credit, both the minerals and the components used in lithium-ion EV batteries must meet new provisions aimed at strengthening the domestic supply chain.
By 2027, 80% of the value of critical minerals in the EV battery must be mined or processed in North America, mined or processed in countries with a free trade agreement with the United States, or recycled in North America.
By 2029, 100% of the value of the components in a battery must be manufactured or assembled in North America. Also key: starting in 2024, electric vehicles that contain battery components or minerals from China and other so-called “foreign entities of concern” will not be eligible for the Clean Vehicle Credit.
These requirements are a big change from the status quo. Up to today, most of the lithium, cobalt, graphite, and nickel used in EV batteries are processed by China and mined in other parts of the world,like the Democratic Republic of the Congo and Australia.
While the United States has some deposits of the needed minerals and there are plans to build refining capacity, the global distribution of minerals and China’s head start suggest that meeting these requirements solely through mining and processing will be challenging.
Luckily, the domestic content requirements of the Clean Vehicle credit can be met in another way: procuring the minerals from recycling battery material.
Right now, the EV battery recycling industry is in its infancy: in fact, most of the lithium-ion battery materials going into recycling plants today do not come from end-of-life EV batteries but rather from scrap material created during lithium-ion battery production.
This makes sense, given that most EV batteries produced through 2023 are still on the road. But with the Inflation Reduction Act potentially adding 37 million EVs on the roads between 2023 and 2032, recycling end-of-life EV batteries will take on new urgency.
It is also worth mentioning that collecting and ultimately recycling EV batteries as they leave the roads is imperative from both an environmental and health perspective.
Indeed, if improperly disposed, the batteries could cause fires or contaminate lands and waters with toxic chemical substances. Failure to recycle EV end-of-life batteries will also be an economic loss when considering the valuable materials they contain, such as cobalt or nickel.
An important piece of information, therefore, is whether the U.S EV battery industry is ready for the upcoming challenges. In an effort to answer this question, we gathered information about operational and announced recycling capacity as of September 2023 from news articles and press releases.
An interesting observation is that recycling plants are being built in regions where EV and lithium-ion battery production sites are already located. This creates a coherent ecosystem where the recycled material can easily be fed back into the lithium-ion battery and EV production lines.
When adding up the annual capacities of all the lithium-ion battery recycling plants that were operational by the end of 2022, we see that at least 105,150 tons of minerals can be recycled annually.
This is sufficient material to produce 220,300 electric car batteries each year, assuming that the average EV battery weighs about 1,000 pounds.
However, if announced recycling plants as of September 2023 are also taken into account, a recycling capacity of at least 652,293 tons per year could be expected by 2030. That’s sufficient to handle about 1.3 million end-of-life electric car batteries annually.
The figure below highlights installed U.S. recycling capacity in 2023 and expected capacity in 2030 compared to the tons of end-of-life batteries that could become available for recycling in the country.
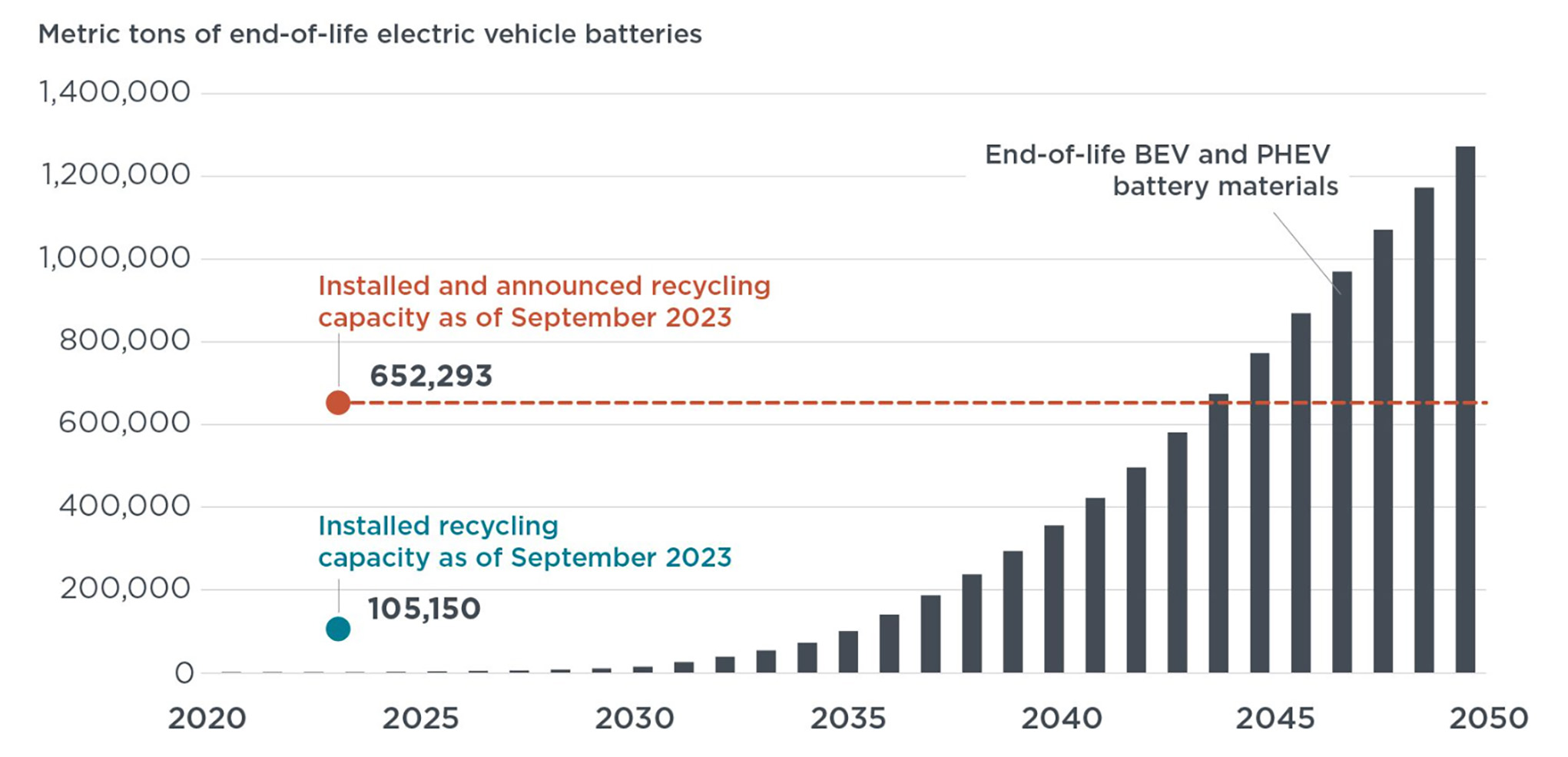
These numbers were determined from projected EV sales and vehicle lifespans following the same methodology as described in our study on scaling up the reuse and recycling of EV batteries.
The weight of end-of-life batteries is approximated using selected materials critical to lithium-ion batteries: cobalt, lithium, manganese, nickel, iron, phosphorous, graphite, copper, and aluminum.
We see from the figure that the 2023 operational recycling capacity should be sufficient to process end-of-life batteries from BEVs (battery electric vehicles) and PHEVs (plug-in hybrid electric vehicles) up to the year 2036.
When recycling plants announced as of September 2023 are included, sufficient capacity is available to recycle end-of-life batteries until 2044.
Not shown in the figure are the additional tons of recyclable material from battery production scrap. According to analysts at Benchmark, this production scrap is expected to be the main source for recycling plants until 2030, but in the longer term, this will represent a small amount of overall material compared to end-of-life batteries.
Uncertainties at the supply chain level suggest that the battery recycling space could gain momentum globally in the years to come.
While most governments are just starting to think through these issues, our study on battery reuse and recycling found that jurisdictions like California, China, and the European Union are already proposing policies for the responsible handling of end-of-life EV batteries.
In California, for example, the Advanced Clean Car II Regulations (ACC II) require manufacturers to affix permanent labels on batteries to disclose information on their chemistries and other information.
Making battery chemistries and other data more transparent will enable third-party recyclers — not just the original manufacturers — to also contribute to recycling efforts and potentially encourage more innovation in the recycling processes.
In the European Union, the new battery regulation stimulates recycling by requiring that by 2031, all newly manufactured batteries include a certain share of recycled material (e.g., 16% for cobalt and 6% for lithium and nickel).
In China, every EV battery produced or imported is recorded in a database and tracked throughout its lifetime to ensure it gets collected and recycled when it reaches its end of life.
We will continue to monitor and analyze the development of EV battery recycling policies around the globe. Such policies will become increasingly critical—for the environment, human health, and EV supply chains—as tens of millions of batteries reach the ends of their lives.
This is an edited version of an article published first by the International Council of Clean Transportation. You can read the original here.